Implementation and Financing of Energy Audits :
Sitaram Gokul Milks Pvt Ltd
The prominent Nepalese business company, Kedia Organization, known for its diverse ventures in manufacturing encompassing cement, steel, sugar, and dairy, is deeply committed to enhancing energy efficiency. Companies one of the manufacturing verticals – Sitaram Gokul Milks Pvt Ltd has undergone two time Investment Grade Energy Audit facilitated by the Energy Efficiency Centre / FNCCI. Industry has the production capacity of 50 Million litres of milk annually along with cream, butter and ghee, Electrical consumption of merely 5 Million NPR and thermal fuel consumption of about 6.5 Million NPR annually. (as per 2017)
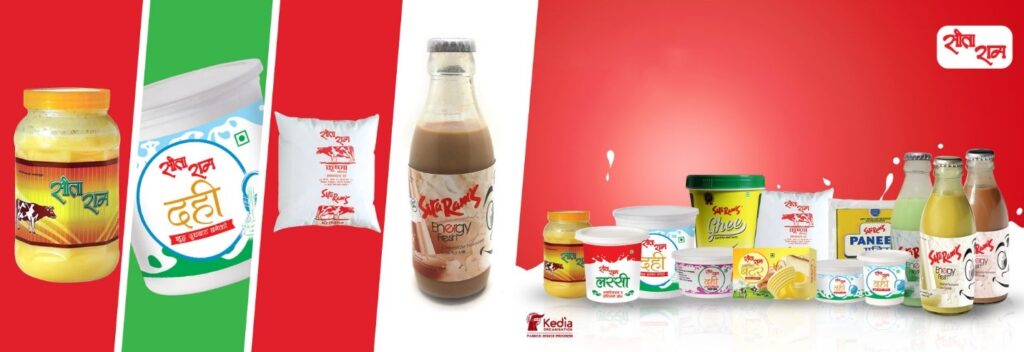
The industry’s different processing units (as shown in the diagram) have received suggestions for five significant ways to save around 44,000 kWh of electricity and 27,000 liters of thermal energy. These improvements would only cost about 5.4 million NPR to implement.
In the main electrical system, it is recommended to add the capacitor banks with auto power factor correction units of about 150 kVAr. The company has duly implemented with an investment of about 300,000 NPR resulting payback period in 38 months.
Similarly, the industry utilized a 1-ton diesel-fired boiler, generating 1640 kg/hr of steam pressure to fulfill its thermal needs in the processing unit. To enhance boiler efficiency and meet the necessary thermal heat requirements, it was advised to replace the current boiler with a more efficient 2-ton boiler. With financial backing from KfW Development Bank, representing the German Federal Government and the Federal Ministry for Economic Cooperation and Development (BMZ), amounting to 7.6 million NPR, and an additional investment of 2 million NPR from the company, the industry has progressed towards greater energy efficiency and got payback in merely 3 years.
Industry is adapting and implementing remaining of the EE options in its yearly action plan. Low cost / No cost Energy conservation practices like operating ground water pump at night shift, Overhauling / maintenance of the air compressor , Boiler and their distributing pipe line with regular insulation wherever required has been regularly attended by management. Likewise medium cost investments such as installation of desuperheater at ammonia compressor discharge, insulation in Ghee boiling pan etc. were enlisted in annual budget plans.